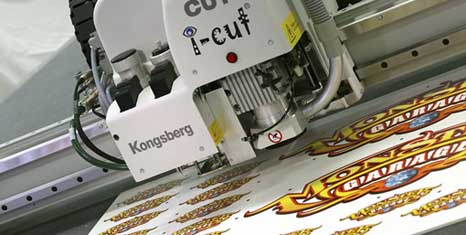
EskoArtwork will demonstrate a comprehensive portfolio of end-to-end workflow and digital finishing solutions at booth 2433 during SGIA Expo 2011, October 19-21, in New Orleans, LA. Solutions to be demonstrated include the Kongsberg i-XP 24, the Kongsberg i-XL 24, and the Kongsberg i-XE 10 Auto finishing systems.
Workstations will offer demonstrations of i-cut Suite, a collection of pre-production tools that streamlines the workflow for narrow format and large-format printers alike, from prepress to finished product — highlighting new automated capabilities offered by i-cut Automate.
i-cut Automate helps complete the i-cut Suite workflow
i-cut Suite offers companies that drive narrow or large format digital printers and/or digital finishing systems professional tools to streamline their workflows — the first workflow offered sign & display shops a complete, integrated solution. Introduced in 2010, the i-cut Suite has seen rapid popularity throughout the world.
Launched at SGIA Expo 2011 is i-cut Automate the latest addition to i-cut Suite, built on EskoArtwork's highly successful Automation Engine. i-cut Automate ties the pieces of the i-cut Suite together, automating the entire production process from design to print to cut. Users can build dynamic workflows that will automate repetitive prepress tasks, thereby enhancing productivity, reducing operator intervention and errors, and saving valuable time, money and materials in the production process.
i-cut Suite components include:
- i-cut Preflight handles efficient preflighting and editing of incoming PDF files, ensuring that jobs will RIP and print correctly. It also lets users make any corrections working within the PDF file.
- i-cut Layout is a module for interactively building and editing sheet layouts, ensuring that jobs are set up to make the optimum use of the substrate through intelligent true shape nesting and tiling. It also enables file preparation for printing, through adding grommet marks, and creating cut paths and bleeds.
- i-cut Vision Pro makes sure that die-less cutting contours match printed images perfectly. Often, slight distortions between printed graphics and contour cut may cause unacceptable results. i-cut Vision Pro registers the actual dimensions and positions on the printed result. Then, finishing is adapted to the shape of the graphics. Added to i-cut Vision Pro earlier in the year was patent-pending Adaptive Registration, a feature that intelligently reduces the number of registration marks read throughout production, increasing productivity without sacrificing accuracy. Another new feature is the ability to automatically eliminate overcuts in sensitive materials such as foam, Reboard and PSA film, by cutting away from inside corners.
With i-cut Automate, all of these functions can be automated in a single workflow, with less operator intervention required and fewer potential manual errors. Through Mac or PC based clients, operators can easily monitor the workflow and interact when necessary through a comprehensive checkpoint. Repetitive tasks are far less time-consuming through dynamic workflows that are easy to set up and operate in a client-server environment. i-cut Automate can also be integrated with Management Information Systems, enabling automatic job creation and the submission of job parameters to the workflow via XML data.
Users with more specific requirements can easily add supplementary modules: a structural design module to allow integration with all standard structural design programs; a graphics preparation module to create the cutting contour on both vector files and images; and a true shape nesting module offering a powerful, true shape nesting solution, particularly for irregular shapes.
The Kongsberg i-XP24: the world’s fastest digital finishing system
On display at SGIA is the Kongsberg i-XP 24, the world’s fastest digital finishing system. The i-XP helps turn short-run POP / POS displays work into profitable, value added jobs, helping sign and display shops offer their customers on-demand production with just-in-time delivery. The Kongsberg i-XP series provides a fast, flexible and highly reliable solution for short run production. With a maximum working area of 87”x126” and a maximum speed of 66” ips (inches per second), the i-XP series can convert a wide range of board, sheet and roll materials. Demonstrated at SGIA is an optional conveyor extension is available that can work with rolls or sheets/boards with an Auto-Feeder with scissor-lift and transfer cart system, expanding the quantity of print runs that can be pre-stacked. The seamless workflow no longer requires an operator to restack or transfer materials.
Kongsberg i-XL 24: Perfect for signs and displays
The Kongsberg i-XL 24, the workhorse of the product line and best-selling Kongsberg finishing system among sign and display companies, offers a comprehensive finishing solution for the widest range of materials, providing automation, high productivity and outstanding precision. The i-XL family, with a maximum material size of 87” x 120”, can also be delivered with an optional conveyor extension, along with the Auto-Feeder and scissor-lift system.
Kongsberg i-XE 10 Auto digital finishing system
AT SGIA, the Kongsberg i-XE 10 Auto is equipped with a fully automated sheet feeder and off load stacker, specifically designed for finishing small-format, prototype, sample and short-run digital printed materials – rolls or sheets can be processed. The sheet feeder system automatically loads and places printed materials on the table. The ‘Pick and Place’ automated stacker enables non-stop sorting, neatly stacking finished pieces. The system also automatically separates waste from the finished items. As a result, the machine can run virtually unattended, delivering significant savings on man-hours. The Kongsberg i-XE10 Auto opens opportunities for creative, new applications with irregular shapes or finishing structures. It can handle a maximum sheet size of 35” x 47” at a maximum speed of 52.5 ips.
Kongsberg tables on display at partner booths
EskoArtwork partners Agfa Graphics (booths 935, 945) and HP (booth 919) will both demonstrate complete print and finishing solutions. Agfa Graphics will exhibit the Kongsberg i-XL24 finishing system, while HP will operate the Kongsberg i-XP24 finishing system.
“The best way to add value — and margins — to a sign or display business is to offer 3D capabilities,” comments Bill Hartman, EskoArtwork Vice President, Sign & Display Solutions. “Exciting opportunities are becoming available for companies wiling to invest in workflow systems that offer some of the designing, printing and cutting steps that are unique to us. These software solutions let print providers get to grips with understanding the steps needed for a workflow. And a starter system needn’t break the bank, nor disrupt the production process. On the contrary, they can add exceptional productivity efficiencies, from the designer’s workstation all the way through to the finishing table. It gets even better with the option to fully automate the process. The future for workflows in sign and display companies is certainly gaining momentum.”
For more information about EskoArtwork Sign & Display products, please visit http://www.esko.com/SignandDisplay